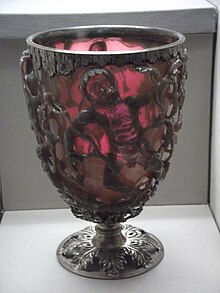
Gyda's saga
An exploration of Historical Glass Bead Making
Monday, February 12, 2024
Historical Pink Glass
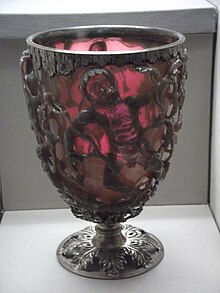
I had a project to complete and the brief for the project was "Historical Glass Beads, "Valentine's Day" theme. My immediate thoughts were "pink" and "love hearts". Neither of these have much evidence across the pre 16th century world, so I decided on "red" and "white", and a couple of love heart shapes on the beads on the premise that feathering and odd shapes do ocasionally turn up.
I thought I might collate any evidence of pink glass here. Any questions or additional sources, please feel free to add.
Wikipedia: Cranberry Glass
https://en.wikipedia.org/wiki/Cranberry_glass
The origins of cranberry glass making are unknown, but many historians believe a form of this glass was first made in the late Roman Empire. This is evidenced by the British Museum's collection Lycurgus Cup, a 4th-century Roman glass cage cup made of a dichroic glass, which shows a different colour depending on whether light is passing through it or reflecting from it; red (gold salts) when lit from behind and green (silver salts) when lit from in front.[2][3] Kitab al-Asrar, an Arabic work attributed to Abu Bakr al-Razi contains one of the earliest modern descriptions of the preparation of gold ruby glass.[4][5]
Tuesday, February 6, 2024
Rock Tumblers and Glass Beads
So for a while now, whilst studying extant museum glass pieces and recreating them, some things haven’t sat quite right.
The shape and the style can be recreated almost perfectly ( warts and all) but the historical glass look and feel is almost clay like. Almost to the point where sometimes it doesn’t look like glass at all.
This is generally explained by weathering and different glass composition and manufacturing tools and furnaces.
My sibling got us a rock tumbler for Christmas. The tumbler mimics the ocean or natural wear and tear over centuries.
0.03 seconds after setting the tumbler on, I had to see what would happen if I stuck some glass beads in there.
So I grabbed a bunch of broken glass, and some random examples that I had previously made and popped them in there with the other rocks that were tumbling away.
Some of the glass ( mostly any of the clear glass) came out as gorgeous sea glass style. But the opaque glass and the Phoenician/ Chinese ones came out EXACTLY like the worn thousand year old clay like glass which was freaking cool to see. They’ve only been in there for 4 days or so, so I’ve chucked them back in to see how it continues to tumble. And it feels so smooth and rounded.
I was asked some interesting follow up questions. Tom asked if I thought the orginal beads were tumbled or equivalent in period or if this was just replicating the act of aging?
I answered with the following:
"I haven’t seen evidence to say it was done initially and on purpose, nor any equipment that says it would have been possible. Based on this I would hesitate to say they were tumbled on purpose.
I have seen evidence where some necklaces were found with hundreds of years of age variations on the one necklace, and wear and tear on beads in ways that suggested constant rubbing and deterioration over time caused by potentially one lifetime.
I would definitely say that this effectively replicates ageing over time based on the very similar look and feel, not only on a surface level but looking more carefully at the details of the deterioration of softer colours ( such as the white)"
Any other questions, please ask :)
Tuesday, July 18, 2023
Building Medieval Furnaces
This post will contain a variety of information including the process of creating the furnaces, the materials and references used, the experience firing and using it , as well as information learnt through experimentation and discussing with others who have previously made these or something similar. I will continue to add to this post as I experiment.
I have been very intrigued by the furnace from Ribe, particularly the recreations done by Thomas Risom. This particular furnace uses the materials found by a riverbed. They are accessible and evidence of the techniques used in this heat receptacle can be found across time and cultures. The other aspect that I am fascinated by is that the shape of this particular volcano furnace allows for high heats, and manipulation by one person, without the need for bellows or others to tend to the fire. It is also small and portable which means I can bring it to events to teach. Amazingly it is also much quieter than modern set ups!
Amusingly, I subsequently found that the experience of working with others was far more enjoyable in good company than doing it solo anyway.
Concepts discovered/Explored
-After 5 hours the coals and the furnace itself were hot enough to get the heat required.
-Coals have been found in extant examples, rather than wood and that makes sense given the above information.
-There are some commonly used structures that produce high heats. Can I combine these with the furnace, to help my heat management? I found out about Swedish fire logs and "Survival/Scout fires. Both of these simply use wood, positioned carefully to create strong air flow. At Festival, we used a small survival/scout fire in camp and out of curiosity I got my glass making tools out. The heat was enough to melt glass. So my theory is, if I build this style within the furnace, not only is it plausible that this would have occured, but it may be effective as well.
-Swedish fire log: https://www.freshoffthegrid.com/swedish-fire-log/
-Scout fire: https://www.fieldandstream.com/articles/survival/fire/2011/01/build-bad-weather-fire/
Materials used:
-Slightly decomposed Horse Poo
-Clay
-Sand
-Hardened clay pot to be removed, instead of willow branch as the structure base.
The Process:
Attempt One |
This furnace produced a fair amount of heat. I used barely any fibers and sediment however, and the next day it promptly cracked. It was too thin, and had too much clay.
Attempt Two |
This furnace construction involved far more clay and sediment, including horse poo for fibers.This is when it was wet. I have placed it on a large cement tile that can be used to transport it.
Composition |
A close up of the composition of the furnace. After discussions with Master Owen, it was clear that my original theory of adding more hay was not the way to go. More fibres was, and it looks much more solid now.
Attempt Two |
This is the furnace when it was dry. I drove this about 300 km for an event.With careful packaging it survived the drive and was used successfully to create a couple of beads. Unfortunately the winds were so strong that we made the decision to move it after we had fired it. Sadly, I had not been able to contain my patience during the week, and it hadn't really gone a proper week of drying and it didn't have enough fibres. As a result, it cracked when moved, the dry parts moving against the rest and falling apart.
Lit up
|
Attempt Three |
Attempt Three (and Four) involved crushing Attempt Two back down, and mixing far more fibres into the mix. I experimented with more diverse fibers that they would have had access to at the time, such as linen, wood dust and hay. As I was doing this, I ended up with a lot more materials than I had previously, so I decided to experiment with a smaller version. Firstly I was curious as to how much heat a smaller version could create, and secondly, I have seen extant examples where the volcano furnace had a carved rock as an extra layer at the top, or something that seemed like a second smaller furnace on top, and I want to see how that affects heat management if I place it on top.
Attempt Four |
The mini version. I am curious to see if this might work, or not. It's small and has less air flow which makes me think it might crack, or not get hot enough. However it may also be quite effective on top of my furnace.
Attempt Three |
After three days of drying, adding sand externally and patting down to remove bubbles and less dense spots. It is drying well , even in the cold Canberra weather, and I hope to fire it up after a week or so.
Attempt Three- Embellishments |
After using a number of different furnaces, medieval and modern I have reached certain conclusions. One being, that if you did this over time and repeatedly, you would make changes to make your life nicer or easier. The indents I have added are places to rest my tools and glass.
This was one of my earlier attempts, which produced some beads. The heat was intense enough about 5 hours in.
I didn't schedule any official classes at Cold War as I wanted to participate in War but also teach organically without a schedule. This worked amazingly in the Bjornhird Makers' Space, as people came in as we worked and asked questions or observed. After some safety briefings, a couple of very interested folk were able to make some beads over the furnace and take them home. I love sharing the joy of glass beadmaking. It's a lot harder than it looks, but the end result is super satisfying!
This was very successful, particularly after the coals had been going for about 5 hours.
After the heat became workable, each bead became easier and easier. The consistency in the bead was on par with the use of modern methods, and adaptation to the particularities of the medieval flame was easy to grasp with some practice.
Ginevra/Gyda Glassmaking
Ginevra/Gyda Glassmaking/Teaching |
Using Master Owen/Sui's Furnace |
This is a dirty hobby! |
Some of the glass beads that were made |
After the heat became workable, each bead became easier and easier. The consistency in the bead was on par with the use of modern methods, and adaptation to the particularities of the medieval flame was easy to grasp with some practice.
Relevant Information:
"In its raw form, glass can be easily worked in a number of ways. Experimentally we have found that it can be directly worked into beads. Using a crucible such as those found at Paviken and Helgo
the raw material can be melted. By reaching into the crucible with a pair of tweezers and slowly drawing the tweezers back a rod of glass can be drawn from the liquid glass. Varying the speed of the draw will change the size of the rod produced. In the archaeological record this produces small lumps of glass with tweezer marks and small stubs of rods attached. These rods can be used to directly create beads in a style strongly related to modern lampworking techniques."
-Glass on Fire
"At Ribe, at least six hearths associated with bead production debris were uncovered.Hearth ÆZ is roughly oval at 53x23 cm. QA is a round lens shaped hearth approximately 50 cm in diameter. The remaining hearths are less well defined. UN is roughly rectangular. UR is irregular in outline.
Bencard et al define these hearths as being of a clay construction but the long section of hearth ÆZ
appears more consistent with a cob construction. Cob has been defined as “a material for walls, made from compressed earth, clay, or chalk reinforced with straw”
-Ribe Excavations
"They are generally rebuilt in the same place after completely demolishing the earlier ones. This results in an abundance of fired-clay fragments with
glass spillage, clay pots, clay plates, arm rings, broken crucibles with a glass layer,
and bricks and other debitage littered around the glassworks."
-Glass Beads in Ancient India
"Furnace designs changed over time but there
were basically two types: tank furnaces and
pot furnaces. Tank furnaces were built with an
integral tank to contain the molten glass. There
is some evidence for smaller tank furnaces being
used in the Roman period in Britain to melt glass
for shaping (Shepherd and Wardle 2009) and a
number of good examples of tank furnaces used
for glass making from the late 19th century"
-Archaeological Evidence
for Glassworking
Furnace Links:
-Thomas Risom: The Bead Maker from Ribe
-https://historicengland.org.uk/images-books/publications/iha-glassworks/heag236-medieval-and-early-post-medieval-glassworks/
-https://www.academia.edu/15486278/Glass_on_Fire_Temperatures_in_reconstructed_Viking_Era_bead_furnaces_in_Can_These_Bones_Come_to_Life_Insights_from_Reconstruction_Reenactment_and_Re_creation_Vol_II
-https://www.cmog.org/article/about-medieval-glass
-https://www.researchgate.net/publication/354986153_BEAD_FURNACES_IN_ANGLO-SAXON_BRITAIN_An_investigation_into_the_likely_sources_of_heat_used_by_beadmakers_in_the_5th_to_7th_centuries_CE
-https://www.researchgate.net/publication/339178110_ANGLO-SAXON_GLASS_BEADMAKERS
-https://exarc.net/keywords/bead
-https://www.archaeology.org/news/10877-221005-ribe-bead-workshop
-https://www.sciencedirect.com/science/article/abs/pii/S2352409X20302790
- Mogens Bencard and Helge Brinch Madsen, Ribe Excavations 1970-1976 Volume 4 (Højbjerg: Jutland Archaeology Society, 1990)
-Heaser, Sue. (2022). BEAD FURNACES IN ANGLO-SAXON BRITAIN An investigation into the likely sources of heat used by beadmakers in the 5th to 7th centuries CE.
-https://museum.wales/collections/online/object/8b8d8c64-392e-3d90-b4e7-ec28749a67c4/Early-Medieval-fired-clay-furnace-lining/?field0=string&value0=finds&field1=with_images&value1=on&page=4
-Glass Beads in Ancient India and
Furnace- Wound Beads at Purdalpur:
An Ethnoarchaeological Approach. https://core.ac.uk/download/pdf/5105475.pdf
-https://historicengland.org.uk/images-books/publications/glassworkingguidelines/heag259-archaeological-evidence-for-glassworking/
Thursday, May 18, 2023
A glass blown Roman Mouse
What ? |
Roman mouse Overall H: 4.7 cm, L: 12.7 cm Also found in blue glass Glassblowing developed in the Syro-Palestinian
region in the early first century B.C. and is thought to have come to Rome
with craftsmen and slaves after the area’s annexation to the Roman world in
64 B.C. The new technology revolutionized the Italian glass industry, these
advantages spurred a rapid evolution of style and form, and experimentation
with the new technique led craftsmen to create novel and unique shapes;
examples exist of flasks and bottles shaped like foot sandals, wine barrels,
fruits, and even helmets and animals[i]
|
||
Where ? |
Rome |
||
When ? |
200-399 BCE |
||
Why ? |
LOOK HOW CUTE AND RANDOM IT IS. Also, I changed the mouse to
give it some slightly more rat like features so that it would fit the
category of “rat”. Unguentaria (tear bottles), and
other small vessels held various oils, perfumes, and cosmetics used by nearly
every member of Roman society.[ii] It holds a surprising amount of liquid. |
||
Evidence |
https://www.cmog.org/artwork/mouse PRIMARY DESCRIPTION: Very
pale brownish yellow, transparent glass, with pale blue streaks; blown,
applied. Animal with object in its mouth. Animal has spheroid head,
constriction at neck, slender pear-shaped body, and slightly upturned tubular
tail with open end, all blown from one pale yellow gather. Tip of tail has
plain rim with rounded lip. Yellow glass has many small bubbles, some of
which are elongated. Eyes, ears, nose, mouth and object carried in it, and legs
represented by blue blobs tooled to appropriate shapes: eyes are small
circular disks; ears are flat semicircles: mouth is single blob tooled to
form jaws, with excess glass pulled up to make nose and with two flattened
blobs of glass, one on top of other, in open mouth; all four limbs are blobs
that have been pinched and in three cases bent at ends to represent feet. Another similar artwork: https://www.metmuseum.org/art/collection/search/257875 |
||
Extra Details |
In the original the glass on
the “mouse’s” face is damaged. The museum says that is carrying something,
but it looks like glass that may have been squished when it was cooling down.
I chose to just make the nose more elongated to look like a rat’s nose. The technique uses
glassblowing, which I am new to. This involves blowing into a metal straw
that has been coated in bead release. This must be done very precisely
otherwise you make exploding glass bubbles. Which is fun. But probably high
on the danger scale. I made this a couple of times and learnt very quickly
how to manage my time and glass without having everything just shatter. The
only thing I would change on this version is the thickness of the tail, but
the thinner I go, the more chance of breaking. I will continue to practice
this. I was happy with the matching of glass colour, and the shape in
general, even though it took a while to get right. |
Reproduction of a Merovingian Necklace
What? 23 monochrome, biconical glass beads from the Merovingian period
Where? Sigmaringen
When? 7th
Century
The original |
My version |
Materials and techniques:
·
Glass
·
· String: Corded string
Images of the process:
Working with Glass:
I have been working on
developing my skill at melting glass and shaping it over the last couple of years.
I have learnt a lot, including where in the flame certain glass must be placed
so that it doesn’t ruin the colour or texture. I have learnt how to steadily
place my hands and rotate both glass and mandrel so that an even amount of
glass, at the right temperature, is kept at the right heat to reproduce the
desired bead.
The necklace presented a
variety of challenges. Glass is a dangerous, sometimes fickle substance, and
certain colours only work properly at a certain heat.
Some of the trickier
techniques (and melting glass onto a mandrel and keeping it even is tricky to
start with!) that I used for this project include:
·
Studying each (photo of) bead in a variety of lights to get
an accurate grasp of the details.
·
Technique of shaping initial bead, then shaping one side,
keeping sides even, and then shaping the other side, whilst keeping everything
even and melting at the correct temperature.
·
Working with tricky colours. These were all tricky. Light
blue flashes (changes colour), red flashes, white burns, green can go red or
brown, yellow gets red markings and the dark blue was a special shade and prone
to melting too hot and reforming with impurities.
· Shaping similar size beads
Details of the equipment and resources:
·
I used a graphite paddle, mandrels, bead release, a knife, fire
annealing and gravity. I try to use the least tools possible and authentic
equipment that would have been used by the glassmakers of the time. Apart from
my fire set-up, all the equipment I have used would have been used at the time
as well.
·
Clear broken glass was often used as well as imported blocks of coloured
glass. (Regia Anglorum)
·
The glass rods I used to recreate these beads were Effetre Murano – 104
COE soft glass rods. This is a close replica of the glass that would have been
used at the time.
·
Bead artisans would have created a small kiln or furnace. The broken
recycled glass would be put into the furnace through holes in the side to melt
in a dish inside the furnace. Air was pumped into the furnace to keep the
charcoal hot. (Guido)
·
I use a hot head torch and MAPP gas. In the future I have plans to
recreate a small portable kiln but melting glass in a small kiln is very
difficult as getting the heat hot enough to melt the glass is a struggle.
·
Metal rods (mandrels) were dipped with a clay mixture called bead
release. The molten glass is wound onto the rod until the desired shape was
achieved. Once the bead size and shape were achieved, a design could be added
by heating thin bits of glass and wrapping them around the bead, with a
“stringer” that was heated and laid on top. (Guido)
·
I use mandrels that would have been very similar to those used, however,
mine are shorter as they don’t need to be as long to reach into a hot fire. The
bead release I use has the crucial ingredients of water, kaolin and alumina
hydrate, which is a composition that would have been used.
·
Beads would then be moved to an annealing dish in the furnace. This
would prevent thermal shock, lowering the chances of the bead cracking.
·
Instead of annealing them in a furnace, I use a product called
vermiculite to allow the beads to cool down slowly. I also use a kiln. In the
future, I would like to try annealing them in a furnace to see what it is like.
· After the beads are finished, I remove them from the mandrels, clean them out with some bead cleaning tools and give them a quick clean with some soapy water.
Future Projects:
·
In the future, I would like to continue to practice more difficult
skills, e.g., fine line work, millefiori use and making the Chinese Warring
state Beads which had over 100 steps each.
·
I am enjoying creating pieces from different times and cultures that
people have never seen, and I will continue to develop my skills by continuing
to choose challenging and unique projects.
·
I also enjoyed working with the museum and the professor when I
recreated a 133 bead Phoenician necklace, and I would like to continue working
with people like this. Not only was it very educational and rewarding, but it
resulted in me contributing to the historical accuracy of the museum- which I
thought was cool! This project led the British museum to writing more specific
information too, which is awesome!
·
I also intend to work on another historical recreation of a glass making
set up.
Primary resource:
https://www.britishmuseum.org/collection/object/H_1908-0801-538
Provenance:
Sigmaringen, Baden-Württemberg, Germany; grave
5, found 1900; associated with 1908,0801.539
Secondary Resources:
Guido, Margaret. The Glass Beads of Anglo-Saxon
England: c. AD 400-700, Boydell Press, 1999.
Holgate, Barbara. “The Pagan Lady of
Peel”, St. Patrick’s Isle Archaeological Trust, 1987.
Regia Anglorum: https://regia.org/
McGloin, Jemma: Of Beads and
Burials: A Microwear and Experimental Study of Early Medieval Glass and Amber
Beads from the Merovingian Site of Lent-Lentseveld.
Subscribe to:
Posts (Atom)